About Alcast Company
About Alcast Company
Blog Article
Alcast Company Fundamentals Explained
Table of ContentsThe smart Trick of Alcast Company That Nobody is Talking AboutHow Alcast Company can Save You Time, Stress, and Money.The Greatest Guide To Alcast CompanyAlcast Company - An OverviewThe Ultimate Guide To Alcast CompanyUnknown Facts About Alcast Company
The subtle difference hinges on the chemical content. Chemical Comparison of Cast Light weight aluminum Alloys Silicon advertises castability by lowering the alloy's melting temperature and boosting fluidity during spreading. It plays an essential role in allowing elaborate molds to be filled up precisely. Additionally, silicon adds to the alloy's stamina and wear resistance, making it useful in applications where toughness is important, such as automotive parts and engine components.It likewise improves the machinability of the alloy, making it less complicated to refine right into completed products. In this method, iron adds to the total workability of aluminum alloys. Copper boosts electrical conductivity, making it useful in electric applications. It likewise boosts corrosion resistance and adds to the alloy's total toughness.
Manganese adds to the toughness of light weight aluminum alloys and boosts workability (Aluminum Castings). It is typically utilized in functioned light weight aluminum products like sheets, extrusions, and profiles. The presence of manganese aids in the alloy's formability and resistance to breaking during manufacture procedures. Magnesium is a light-weight aspect that provides strength and effect resistance to aluminum alloys.
About Alcast Company
Zinc boosts the castability of light weight aluminum alloys and aids control the solidification procedure during spreading. It enhances the alloy's toughness and solidity.
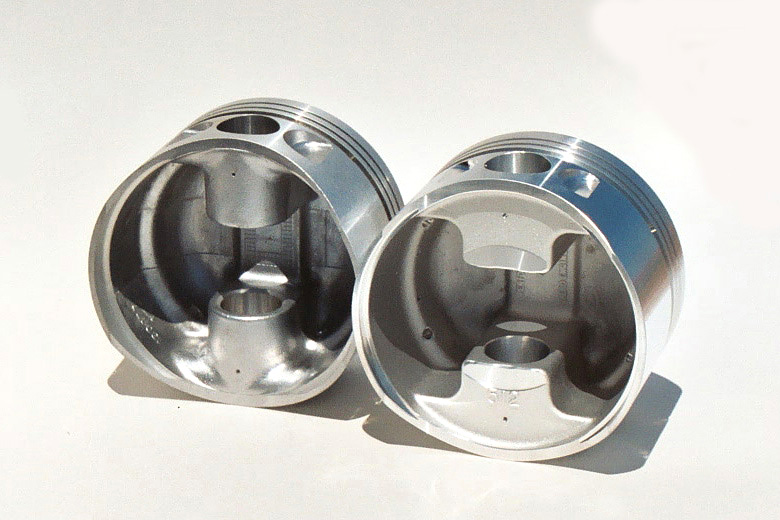
The main thermal conductivity, tensile toughness, return stamina, and elongation differ. Select ideal raw products according to the performance of the target product generated. Among the above alloys, A356 has the highest possible thermal conductivity, and A380 and ADC12 have the least expensive. The tensile restriction is the opposite. A360 has the very best return toughness and the greatest elongation rate.
Some Known Facts About Alcast Company.
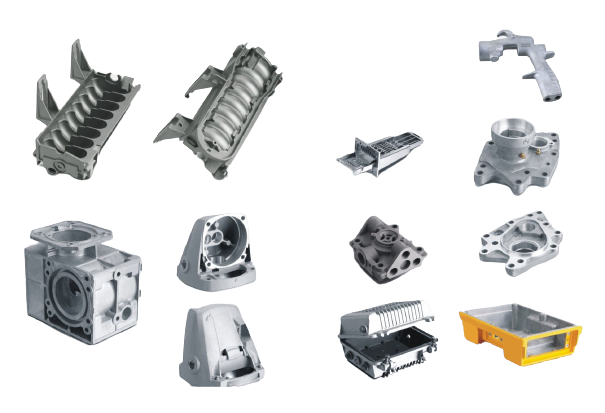
In precision casting, 6063 is fit for applications where detailed geometries and high-grade surface area coatings are vital. Examples consist of telecommunication enclosures, where the alloy's exceptional formability permits smooth and cosmetically pleasing layouts while preserving structural integrity. Similarly, in the Illumination Solutions sector, precision-cast 6063 parts produce elegant and effective lights components that require complex forms and great thermal efficiency.
The A360 shows exceptional prolongation, making it ideal for facility and thin-walled parts. In precision spreading applications, A360 is fit for industries such as Customer Electronic Devices, Telecommunication, and Power Tools.
5 Easy Facts About Alcast Company Described
Its special properties make A360 a useful selection for accuracy casting in these industries, improving product sturdiness and quality. Light weight aluminum alloy 380, or A380, is a commonly utilized casting alloy with a number of distinct qualities. It offers exceptional castability, making it a suitable choice for accuracy spreading. A380 exhibits great fluidity when molten, making sure detailed and in-depth molds are properly recreated.
In accuracy spreading, light weight aluminum 413 shines in the Customer Electronic Devices and Power Tools industries. It's commonly used to craft elaborate components like smartphone housings, electronic camera bodies, and power tool casings. Its accuracy is exceptional, with tight resistances as much as 0.01 mm, making certain flawless product assembly. This alloy's exceptional deterioration resistance makes it a superb selection for outside applications, making certain long-lasting, resilient products in the stated sectors.
Some Known Questions About Alcast Company.
As soon as you have decided that the light weight aluminum pass away casting procedure is suitable for your job, a critical following action is choosing one of the most proper alloy. The light weight aluminum alloy you select will considerably impact both the spreading procedure and the properties of the last product. As a result of this, you need to make your decision very carefully and take an enlightened strategy.
Figuring out the most suitable light weight aluminum alloy for your application will certainly imply weighing a vast selection of features. The first category addresses alloy attributes that affect the production process.
Alcast Company Can Be Fun For Anyone
The alloy you select for die spreading directly impacts numerous aspects of the spreading process, like just how very easy the alloy is to function with and if it is susceptible to casting flaws. Warm breaking, likewise understood as solidification breaking, is a typical die spreading flaw for light weight aluminum alloys that can cause interior or surface-level splits or splits.
Specific aluminum alloys are much more vulnerable to warm splitting than others, and your visit our website option needs to consider this. An additional typical defect located in the die casting of light weight aluminum is pass away soldering, which is when the actors stays with the die walls and makes ejection tough. It can damage both the cast and the die, so you need to seek alloys with high anti-soldering residential or commercial properties.
Deterioration resistance, which is currently a notable quality of aluminum, can differ substantially from alloy to alloy and is a vital particular to consider depending on the ecological conditions your product will be exposed to (aluminum casting manufacturer). Wear resistance is an additional residential or commercial property frequently looked for in aluminum products and can differentiate some alloys
Report this page